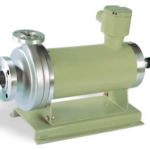
Top 5 Advantages Of Using Centrifugal Canned Motor Pumps In Industrial Applications
September 23, 2024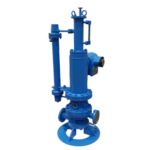
Top Benefits Of Using leak free pumps In Industrial Applications
September 25, 2024Managing industrial pumps and motors involves technologies that need to be understood in terms of operating safety, including concerns about overall productivity and employees. Hydrodyne Tiekoku India Pvt. Ltd is a leading company that offers solutions in Industrial Pump And Motor operations, and one of the main aspects we consider when providing the solutions is safety.
1. Proper Installation and Alignment
The first key factor in the safe use of industrial pumps and motors then is installation. Installing incorrectly results in misalignment, which results in vibration and wearing down of the equipment and may, at one point, fail to perform as it was manufactured to do. It is, therefore, important that the pump and motor are positioned correctly at the time of installation. When alignment is not achieved, it is also postulated that these systems may suffer energy losses and become less efficient. Hence, having specific precision tools for checking and making some realignments before commencing operation is an essential precautionary measure to exercise.
2. Regular Maintenance and Inspections
It is essential to constantly service and check for any anomalies that may lead to significant problems in the future. This would involve carrying out tests for signs of wear and tear, possible leakage, strange sound and vibration. A maintenance log can also be used to record the status of the pump and motor for a certain period of time so as to be in a position to replace or repair them if they are worn out. Inspections also guarantee that numerous safety systems, including pressure relief valves and emergency shut-down systems, are in good working condition, thereby preventing possible mishaps that might occur.
3. Understanding Operating Limits
All motors and industrial pumps have their limits under which they operate, such as pressure, temperature, and flow rate. The levels should not be exceeded as this results in catastrophic failure with associated high risk to safety. It is necessary for the operators to know the limitations of the equipment and must refrain from going beyond them during its usage. An overload of the pump or a motor of the electric equipment can result in overheating of the equipment and thereby lead to fire outbreaks or even explosions.
4. Training and Certification of Operators
Training and certification of the operators as a means of laying down the needed knowledge and expertise on the part of the operators in handling Industrial Pumps And Motors are also very crucial. These should include regular operation of the pumps and their related motors, safety measures in handling the equipment, measures to take during an emergency, and features specific to individual equipment. Further, it will be helpful to conduct repeated refresher courses and practical training sessions to keep the operators abreast of the modern tendencies in the issue of personnel protection.
5. Emergency Shutdown Procedures
Proper and well-understood EPS, as it applies to a particular piece of equipment or an operating process, is critical, especially in the event of a failure or a dangerous condition. Training for all the operators should be done on these procedures; hence, all understand the proper measures to take in case of an event that may lead to the equipment being shut down safely. This is information about where the Emergency Stop Buttons are situated, how depressurization is executed, and other things that may be needed in order to make the piece of equipment safe in case of an Emergency.
6. Use of Personal Protective Equipment (PPE)
Since PPE is one of the primary measures for workplace safety, it is crucial to find out how organizations handle its usage. First of all, it is recommended that operators put on the appropriate PPE, such as gloves, safety glasses, ear protection, and steel-toed boots, before they operate the industrial pumps and motors. Where fluids or other chemicals of a dangerous nature are flowing, extra safety gear such as gloves, unique jackets, and face masks may be required.
7. Monitoring and Control Systems
In the present day, Industrial Pumps And Motors incorporate sophisticated monitoring and controlling devices. These systems can give timely information on the status of the operation, such as operations such as assurance and temperature or vibration. When such data is closely observed, the operators are able to observe that there is something wrong and take the necessary action before the situation becomes a safety hazard. Automated control systems also have safety benefits by modifying the use conditions on the operating equipment in response to changes in the environment.
Conclusion
Appropriate measures that should be taken to ensure the safe operation of the industrial pumps and motors include the correct installation, proper maintenance, training of the operators, and correct safety measures. Through these safety considerations, industries can reduce the dangers and achieve the goal of expanding the life of the equipment used in sectors while at the same time enhancing the safety of the personnel. Hydrodyne Tiekoku India Pvt. Ltd. ensures the delivery of industrial pumping solutions that are used by local drivers and passengers in every application.