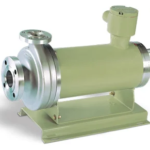
Revolutionizing Industrial Processes: The Advantages of Hermetically Sealed Canned Motor Pumps
August 5, 2024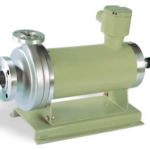
Beyond the Basics: Advanced Features of High-Performance Canned Motor Pumps
August 11, 2024When choosing the right pump, one should consider some crucial factors to make the right decision regarding the type of pump to purchase, the design, and the manufacturer. Canned motor pumps are widely used in different high-pressure industrial processes because of their dependability and performance. Numerous Canned Motor Pump Manufacturers produce pumps for high-pressure applications.
But how can you know if the pump you’re choosing will provide you with all the potential and required benefits? No worries! In this article, we will focus on the factors that one needs to take into account when selecting the most suitable canned motor pump for high-pressure operations.
Understanding Canned Motor Pumps
Canned motor pumps are seal-less pumps that have a motor and pump in the same housing with no leakage seal between the two. This innovative design also does not have the shafts that are usually required to be sealed, which greatly reduces the potential for leakage and maintenance. These pumps are useful in dealing with dangerous, poisonous, and erosive fluids that are useful in high-pressure processes in chemical, oil, and electricity-generating companies.
Key Features and Benefits
1. Sealless Design
Because canned motor pumps have no shaft seals, leakage, which may be fatal with hazardous or toxic fluids, is impossible. This feature is useful for increasing safety and decreasing the impact on the environment.
2. High Reliability
It is imperative to note that canned motor pumps are some of the most reliable and long lasting equipment in the industry. Mechanical seals are not used in this equipment and this eliminates the continuous wearing that is usually associated with pumps hence there is longer service time and less time off operations.
3. Low Maintenance
Canned motor pumps have fewer parts in operation and no mechanical seals hence they are easier to maintain as compared to conventional pumps. This results in reduction of costs of maintenance and improvement of working conditions and productivity.
4. Compact and Space-Saving
This feature makes canned motor pumps small in size and hence take less space and this is favorable for installations that have constrained space.
Factors to Consider When Choosing a Canned Motor Pump
1. Fluid Characteristics:
It is essential to comprehend the characteristics of the fluid being pumped. Take into account the temperature, corrosiveness, viscosity, and possibility of solid particle presence in the fluid. These elements will affect the design and choice of materials for the pump.
Viscosity: The degree of viscosity varies throughout fluids and influences how well the pump can move the fluid. Higher resistance pumps are needed for high-viscosity fluids.
Temperature: The material and design of the pump can be affected by the fluid’s temperature. Elevated temperatures may require certain materials or cooling systems.
Corrosiveness: Selecting the appropriate material for the pump is crucial to preventing damage and guaranteeing longevity if the fluid is corrosive.
Solids Content: Pumps equipped to handle abrasives without clogging or over-wearing are necessary for fluids containing solid particles.
2. Pressure and Flow Requirements
Accurately determine the pressure and flow requirements of your application. Various Canned Motor Pump Manufacturers have products available in various configurations to handle different pressure levels and flow rates. Ensure that the pump you choose can meet the demands of your specific application.
Pressure Levels: Different applications require different pressure capabilities. Understanding the maximum and minimum pressure requirements will help in selecting a suitable pump.
Flow Rate: The pump’s flow rate must align with the needs of your application to ensure efficiency and effectiveness.
3. Harmony of Materials
The fluid being handled must be compatible with the materials used to build the pump. Stainless steel, Hastelloy, and other alloys resistant to corrosion are common materials. The longevity of the pump may be ensured, and corrosion can be prevented by using the right materials. Because of its strength and resistance to corrosion, stainless steel is frequently utilized.
Hastelloy: Fit for conditions that are extremely corrosive.
Additional Alloys: For certain applications, certain alloys could be needed to give the appropriate resistance and endurance.
4. Range of Temperature
Think about the application’s operating temperature range. The durability and effectiveness of the pump can be impacted by high temperatures. Make sure the pump you choose can withstand the process’s temperature extremes.
Thermal Expansion: Materials may expand at high temperatures, which could have an impact on the pump’s functionality.
Cooling Requirements: Some applications may need additional cooling mechanisms to maintain optimal pump performance.
5. Efficiency and Energy Consumption
An important consideration when choosing a canned motor pump is energy economy. To cut operating expenses, look for pumps with excellent efficiency and low energy use. Contemporary canned motor pumps are engineered with cutting-edge technologies to improve energy economy.
Energy Costs: Over time, energy-efficient pumps save a substantial amount of money by using less energy.
Environmental Impact: Reducing energy use also means lessening one’s environmental impact, which is consistent with sustainability objectives.
6. Setup and Upkeep
Consider how simple it is to install and maintain. Certain pumps could need specific equipment or knowledge to install and maintain. Choosing a pump with easy installation and low maintenance needs is the best option.
Complexity of Installation: Select a pump that may be readily installed without requiring significant adjustments to the current systems.
Maintenance Needs: Pumps with fewer moving parts and simpler designs typically require less maintenance, reducing downtime and costs.
7. Compliance and Certifications
Verify that the canned motor pump from the particular manufacturer satisfies all applicable industry certifications and norms. Adherence to established benchmarks like API, ANSI, and ISO guarantees that the pump satisfies quality and safety standards.
API Standards: Ensures the pump meets the American Petroleum Institute’s standards for performance and reliability.
ANSI Standards: Compliance with the American National Standards Institute’s guidelines guarantees quality and safety.
ISO Certifications: International standards ensure that the pump meets global quality and safety benchmarks.
Conclusion
It is important to carefully evaluate a number of variables when selecting a canned motor pump for high-pressure applications, including fluid characteristics, required pressure and flow, compatibility with materials, temperature range, efficiency, installation, and adherence to industry standards.
Choose Hydrodyne Pumps to learn more and get professional advice. They are a top Canned Motor Pump Manufacturer that has a variety of superior pumps designed to satisfy various industrial requirements.