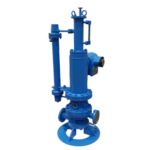
Top Benefits Of Using leak free pumps In Industrial Applications
September 25, 2024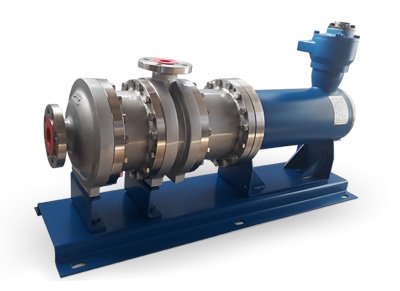
Top 5 Advantages of Using Multistage Pumps in Industrial Applications
October 14, 2024Chemical Pumps are essential in providing safe and efficient operations handling across industries such as chemical, pharmaceutical, and food processing industries. These pumps are applied where a solution needs to be pumped that is corrosive, hazardous, or very viscous that cannot be handled by ordinary pumps.
These specialized pumps prove helpful in industries that involve the safe and accurate transfer of fluids. Hydrodyne Tiekoku India Pvt. Ltd., an acclaimed company in the pumping sector, respects the role that chemical pumps play in ensuring safety and productivity.
The Importance of Chemical Pumps in Industry
Chemical pumps are widely used in industries where it is necessary to transfer and handle aggressive or hazardous material, etc. These pumps are designed to handle chemical and abrasive characteristics of the products they will come across in their working processes to avoid loss of pump total efficiency. Chemical Pumps do not leak or spill like other pumps. This is crucial in ensuring that there is no environmental pollution and protecting the lives of people working in chemical plants and industrial companies.
Types of Chemical Pumps
There are several types of chemical pumps, each suited to different industrial applications based on the properties of the fluids they are designed to handle:
- Centrifugal Pumps: These are used extensively due to their ability to handle large volumes of fluids at high flow capacity. Centrifugal pumps are suitable for handling low-viscosity fluids and are widely used in industries such as water treatment, chemical and oil industries.
- Positive Displacement Pumps: These pumps are ideal for products that are thick or contain some small particles. They are popular, especially in food and beverage applications or pharmaceutical chemicals, as well as in any application that demands accurate flow.
- Diaphragm Pumps: As for the leakages, these have been proven to be leak-proof and are often used in industries where containment of dangerous fluids is paramount. These pumps can effectively deal with corrosive, abrasive, and toxic chemical products.
Ensuring Safe Operations with Chemical Pumps
Safety is paramount when dealing with chemical pumps, as improper handling of hazardous fluids can lead to catastrophic consequences. Here are some essential safety considerations:
- Material Compatibility: Pump material selection is also critical to avoid corrosion and degradation of the equipment. It is essential that the wetted components of the pump are compatible with the chemicals to be handled to prevent reactions that may harm the unit. This flows through common materials used in the construction of process equipment, such as stainless steel, Teflon, and other corrosion-resistant alloys.
- Proper Installation: Chemical pumps follow several basics; hence, it is essential to ensure that they are installed correctly. This encompasses correct positioning, locking or fastening couplings, and the proper selection of a suitable pump for the process in question. Any incorrect alignment can cause seepage, rubbing, and wearing and ultimately lead to problems with the pump.
- Regular Maintenance: The chemical pumps should undergo regular maintenance in order to enhance their general performance. It is recommended that regular inspections are done to detect signs of wear, corrosion, or other potential problems before they result in failures. Maintenance also requires the replacement of seals, gaskets, and all other relevant parts which tend to wear out.
- Monitoring and Control Systems: Modern instrumentation facilitates the monitoring of the performance of chemical pumps whereby data such as pressure, rate of flow, and temperature can be obtained in real-time. These systems help the operators to recognize possible issues with the equipment and take necessary actions on time to avoid an accident or damage.
Applications of Chemical Pumps
Chemical pumps are used in a variety of industries, each with specific requirements:
- Chemical Processing: These pumps are essential in handling and moving acids, bases, solvents, and other aggressive fluids that are used in manufacturing.
- Water Treatment: Chemical pumps are used to introduce and transport chemicals for treatment to a water system, hence safe and clean water.
- Pharmaceuticals: In pharmaceutical manufacturing, chemical pumps transport, with accuracy, the active pharmaceutical ingredients and solvents in the creation of drug products.
- Food and Beverage: Pumps in the value chain are used to transport cleaning agents, food-grade chemicals, and additives in the production process, and these are safe and meet health standards.
Conclusion
Chemical pumps are essential in ensuring safe operations within industries, mainly where the fluids being transported are dangerous or eroded construction materials. Proper selection of Chemical Pump type, installation, maintenance, and monitoring reduces the probable incidence of an unfortunate event in industries, increasing efficiency. Hydrodyne Tiekoku India Pvt. Ltd. has endeavored to become a leading supplier of chemical pumps that conform to high safety and performance indexes characteristic of present-day industries.