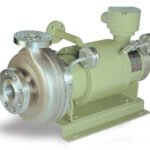
Top Hot Oil Pumps Manufacturers in India (2025): Brands, Types & Selection Guide
May 10, 2025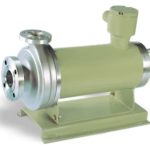
Chemical Pumps: Types, Applications & How to Choose the Right One for Your Industry
May 13, 2025Multistage pumps are a testament to engineering finesse and hydraulic expertise in the complex universe of fluid management. With their grace and efficiency in handling high-pressure applications, these pumps are the behind-the-scenes heroes of most industrial and commercial processes. Whether pressurising water supply over long pipelines or pressing complex boiler feed systems, Multistage Pumps are critical components in innumerable systems. But what about them makes them so versatile and so potent?
Let’s debunk these mechanical wonders, investigate their working mechanisms, identify their types, and analyse the fields where they reign supreme.
What Are Multistage Pumps?
A multistage pump is essentially a centrifugal pump with more than one impeller (or stage) sharing the same shaft. Each stage includes an impeller and a diffuser. The fluid’s energy increases in each stage, which causes a significant rise in pressure with little change in flow rate.
In other words, a Multistage Pump forces fluid through multiple “pressure-increasing” chambers one after another. This makes them especially valuable when one impeller cannot provide sufficient pressure for the desired application.
How Do Multistage Pumps Work?
The working principle is based on centrifugal force. Here’s how it works step by step:
- Initial Intake: Fluid enters the pump at low pressure through the suction port.
- First Stage: The first impeller gives velocity to the fluid.
- Intermediate Diffusers: This kinetic energy is subsequently transformed into pressure through diffusers.
- Sequential Boosting: The pressurised fluid proceeds to the next stage, doing the same with every impeller.
- Final Discharge: The fluid leaves the pump at a much higher pressure than entered.
This multistage boosting of pressure allows multistage pumps to deliver more head than single-stage pumps, where high head is needed.
Types of Multistage Pumps
There are mainly two shaft orientation configurations of multistage pumps:
1. Horizontal Multistage Pumps
Impellers are attached to a horizontal shaft.
Well suited for low vertical space applications.
Typically applied in HVAC systems, boiler feed service, and pressure boosting.
2. Vertical Multistage Pumps
Impellers are centred on a vertical shaft.
Optimised for low floor space utilisation and well-suited for deep well pumping.
Preferred in high-pressure washdowns, water treatment plants, and tall building water distribution.
Moreover, depending on casing construction, multistage pumps may be radial split (for high-pressure, low-flow applications) or axial split (for high-flow, moderate-pressure applications).
Applications of Multistage Pumps
Their special design and performance make multistage pumps a necessity in industries:
Water Supply & Pressure Boosting: Provides uniform pressure in municipal water supply and high-rise buildings.
Boiler Feed Systems: Supplies feedwater to high-pressure boilers in power plants and manufacturing facilities.
Reverse Osmosis (RO) Systems: Pump water through semipermeable membranes at high pressure for desalination.
Mining & Dewatering: Utilised a pump to water from deep shafts and tunnels with heavy-duty capability.
Firefighting Systems: Provides a constant and high-pressure water supply essential for firefighting.
Oil & Gas Industry: Accommodates high-pressure injection and transfer of fluids in upstream applications.
Why Choose Multistage Pumps Over Single-Stage Pumps?
- More Pressure Capability: Multistage pumps can create higher pressures without more motor power.
- Energy Efficiency: Suitable for long-distance fluid transfer and high-rise applications.
- Flexibility: Stages may be added or subtracted depending on pressure needs.
- Smooth Flow Characteristics: Reduces pressure surges and provides a constant output.
Design Considerations When Selecting a Multistage Pump
Engineers need to consider the following before they choose a multistage pump:
- Desired Head and Flow Rate
- Fluid Properties (viscosity, temperature, corrosiveness)
- Installation Footprint (horizontal vs vertical)
- Maintenance Accessibility
- Pump Material and Seal Type
Hydrodyne’s multistage pump line is designed to address these complexities with cutting-edge design, heavy-duty build quality, and unparalleled service life.
Final Thoughts
From skyscrapers to underground mines, Multistage Pumps quietly and dependably get the job done where other pumps can’t. Their capacity to develop pressure through multiple stages without sacrificing efficiency makes them an engineering staple in mission-critical infrastructure and industrial processes.
If you are looking for precision-crafted multistage pumps that guarantee longevity, efficiency, and performance, Hydrodyne Pumps is your go-to company. Discover our extensive array of pumping solutions designed for high-performance applications.
Come to Hydrodyne Teikoku (India) Pvt. Ltd to talk to our experts and get the ideal multistage pump for your requirements.